The construction and military vehicle industry face many challenges. Tracked vehicles must undergo extreme loading, but also need to be safe and ensure comfort for operators. Increased efficiency and more stringent environmental requirements are also important. MotionPort possesses the knowledge and technology to use simulation to help with these demands.
RELATED PRODUCTS
Tracked vehicle simulation:
Interaction with Dry Particles (i.e. Rocks, Grain, etc.):
Suspension and Durability Analysis, Cabin Comfort Studies:
- RecurDyn/TSG (Time Signal Generator)
Mechatronics:
Belt, Chain, and Gear Modeling:
Flexible Body Modeling:
Elasto-Hydro-Dynamic Analysis for Pistons and Bearings:
- RecurDyn/EHD (Elasto-Hydro-Dynamic)
Research Success Stories
Commercial Success Stories
Questions About Tracked Vehicle Solutions?
RecurDyn Motion Simulation Software Simulates Track Loader
Case New Holland compact track loader simulations help manufacturer keep pace with evolving products.
CASE NEW HOLLAND (CNH), a leading agricultural and construction equipment company and part of the Fiat Group, is increasing its motion simulation capabilities as its product designs evolve. One example is the design of compact track loaders that were developed to provide increased traction and reduced ground pressure as compared to traditional skid-steer loaders with tires. The Case 450CT compact track loader shown in the figure has 82 net horsepower (61 kW) with a 3,857-lb. lift capacity.
The addition of a track system adds additional moving components to a compact track loader, including the band track. The flexible behavior of the band track must be taken into account as well as its contact with the front and rear idlers and a number of track rollers. An engineering advantage of using a track system is that only one drive shaft is needed for each side, as compared to the two drive shafts per side that are used to provide the four-wheel drive of a typical skid-steer loader.
The undercarriage of the compact track loaders incorporates features that CNH developed in their many years of experience with large excavators and crawler dozers. The affected components include the track, rollers, idlers, seals, track tension adjustment, and final drives. For example, the loader features track rollers with three flanges and two sets of center-guide lugs on the track in order to prevent de-tracking when the loader is operating along the side of a slope.
The development of a durable tracked vehicle requires load data for the track components and the track structure. Physical testing of a compact track loader is challenging because it is difficult to instrument the track due to track flexing and the contact with undercarriage components. Instrumentation is further complicated by the debris in contact with the undercarriage during testing in soil conditions. CNH developed a special test track for impact loading by creating a grid of pipes that the loader would traverse. The pipes are located to apply various combinations of loads on the left and right track assemblies.
See the rest of this case study, published in Desktop Engineering.
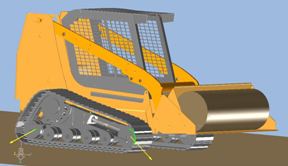

These two figures show outputs that are obtained from the RecurDyn simulations (see below for animations). The upper figure shows the loads on the front and rear idlers during a pivoting maneuver. The yellow arrows indicate the vector force on the hubs and the green arcs indicate the torque acting on the hubs. The lower figure shows the forces at two nearby track rollers as the loader traverses a half-round obstacle.
More Information
- Learn about RecurDyn/LM-Track (Low-Mobility Track Toolkit) which was used in this case study.
- Request more information about this and other case studies.
Simulation Digs into Large Excavator Models
A new approach to rigid-body simulation lets engineers with Hitachi Construction Machinery (HCM), Tokyo, model motions of off-highway vehicles that typically don’t have shock-absorbing suspension systems.
Instead, impact and vibrations are absorbed by the equipment’s flexible steel frame. RecurDyn dynamic analysis software from FunctionBay Inc., Ypsilanti, Mich. (www.functionbay.com) uses a recursive approach to generate equations of motion and relative coordinates that represent the construction equipment.
Complex rigid bodies would seem ideal for multibody simulation software. But conventional multibody programs typically have a difficult time contending with the large number of rollers, joints, linkages, and other parts touching one another in track assemblies. The process of modeling many parts and defining interconnections separately is tedious and time consuming with conventional software. In addition, conventional simulations tend to behave erratically during the lengthy simulation runs.
The mathematical approach in RecurDyn simplifies the simulation, minimizes analysis time, and still preserves model detail. The software even handles intermittent contact from the vehicle’s bending and twisting. Toolkits for special-purpose analyses, as for tracked vehicles, let users quickly build and solve complex models.
According to HCM engineer Akio Hoshi, “Design engineers as well as expert analysts can build models for dynamic analysis using toolkits in the software. Even relatively untrained engineers can complete sophisticated models in a week or so.”
— Paul Dvorak
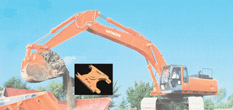
Dynamic simulation refined the design of this tracked excavator to minimize shock and vibration.
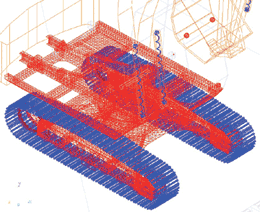
Tracked excavators have about 200 rigid-body parts such as sprockets and track links. The frame of the elastic model has about 16,000 nodes.
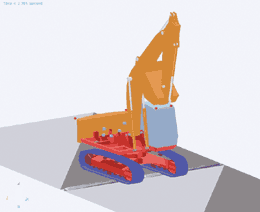
A simulation of an excavator moving over rough terrain shows the body rocking from vibrations.
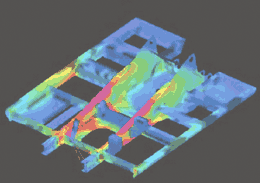
Dynamic stress distribution on the main frame stems from structural analysis based on RecurDyn output load data.
More Information
- Learn about RecurDyn/LM-Track (Low-Mobility Track Toolkit) which was used in this case study.
- Request more information about this and other case studies.