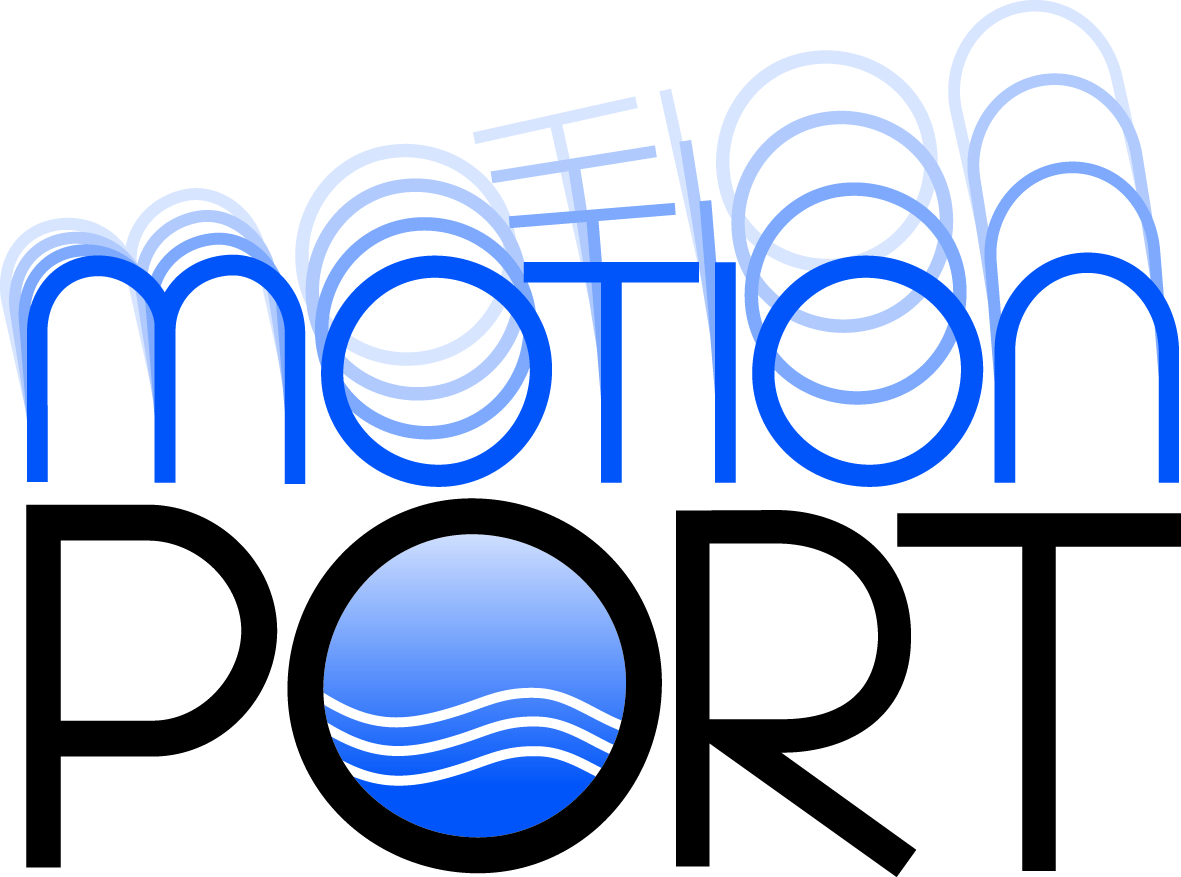
Better Engineering Through
Multibody Dynamic Simulation
June 2019 | Issue #19
In This Issue:
• New Tutorial: RecurDyn & Particleworks Co-simulation with FFlex Bodies
• MotionPort Supports Technology Events at Local University
• Reminder about the Upcoming RecurDyn Users Conference
• User Tip: Using the ‘Scenario’ Simulation Option
New Tutorial about the new RecurDyn
V9R2 capability to include FFlex bodies in co-simulations with Particleworks
In earlier version of RecurDyn and Particleworks the fluid particles could only interact with rigid bodies. Now, RecurDyn V9R2 has the capability to include FFlex bodies in co-simulations with Particleworks. An interesting tutorial uses the example of a styler steam clothing care system to teaches how to perform a co-simulation between RecurDyn and Particleworks. The co-simulation illustrates the dynamic interaction between the shaking mechanism and the flexible bodies (representing the clothes) in RecurDyn and the fluid particles of Particleworks that represent the steam.
The styler unit, shown in the image, is used to shake off the dust attached to cloth and to remove its wrinkles with steam. It also reduces the odors and allergens in the clothing.
The tutorial analyzes the dynamic interaction between an item of clothing, which is expressed as a flexible body, and the steam, which is expressed as particles.
After the co-simulation, an analysis is made of the stress in the clothing as the particles touch the flexible body, using the Contour function of RecurDyn.
To learn more about the styler unit, perform a search on your favorite search engine using the text: “styler steam clothing care system.”
MotionPort plans to create additional examples of this new capability, both with Particleworks and EDEM. If you have an application of interest, please let us know. The best idea for both the Particleworks and EDEM examples will be selected and the corresponding tutorials will be created. To send your examples, please enter them on our Contact Us page.
Click play below to watch the video (approx. 9:38).
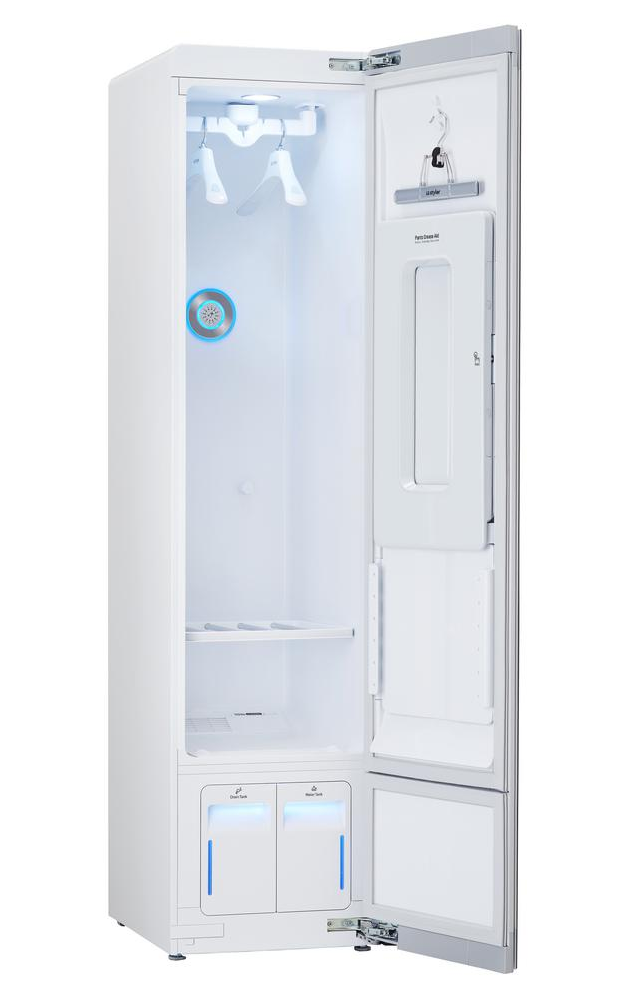
The Styler co-simulation video below covers the following topics (with time stamps): Creating walls (0:30), Exporting walls (1:55), Creating steam particles (2:16), Setting fluid properties (3:26), Co-simulation (7:32), Post-processing (8:45)
MotionPort Supports Technology Events at Local University
Regional Symposium for Research, Innovation and Creativity
Dixie State University (DSU) and the Undergraduate Research Office in St. George, UT hosted the third annual Regional Symposium for Research, Innovation, and Creativity, in April 2019.
This Symposium is a forum to present cutting-edge research, innovation and creative projects in various formats, including talks, posters, performances, and displays. Students, faculty, staff, and members of the Southern Utah community were invited to submit abstracts and participate in this event.
Brant Ross of MotionPort participated again in this year’s symposium with his presentation:
Simulation of Dust Accumulation and Removal on Martian Solar Arrays
This presentation was based on MotionPort’s most recent NASA Small Business Innovation and Research (SBIR) Phase I submission.
Dust accumulation is a serious design risk for sustained solar power on Mars because dust accumulation reduces the power output of solar arrays over time.
MotionPort developed processes and best practices to simulate dust accumulation and removal.
The model simulated was based upon the Compacting Telescoping Surface Array (CTSA) concept.
The NASA reviewers were very impressed with MotionPort’s research results, saying that they “had never seen such simulation capabilities before.”
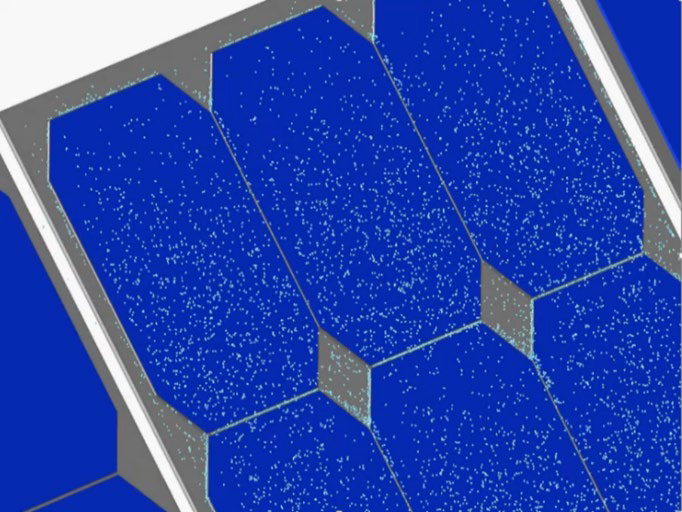
MotionPort is pleased to continue its support of local resources for Design, Engineering and Manufacturing both in the school systems and in the surrounding community.
Mechanical Engineering Student Competition
MotionPort headquarters is located in St. George, Utah, which is home to Dixie State University. DSU recently started a Mechanical Engineering program. The final major project of the “Introduction to Design and Prototyping” class was a design competition in DSU’s 1st Annual Dixie Design Day.
Teams of 3 to 5 students were tasked with building a themed putting green that the public would be allowed to play.
The students had three opportunities to impress:
• official judging by our own Brant Ross (sponsor and judge)
• faculty evaluation by DSU Engineering Department professors David Christensen and Trevor Terrill
• voting by players from the community.
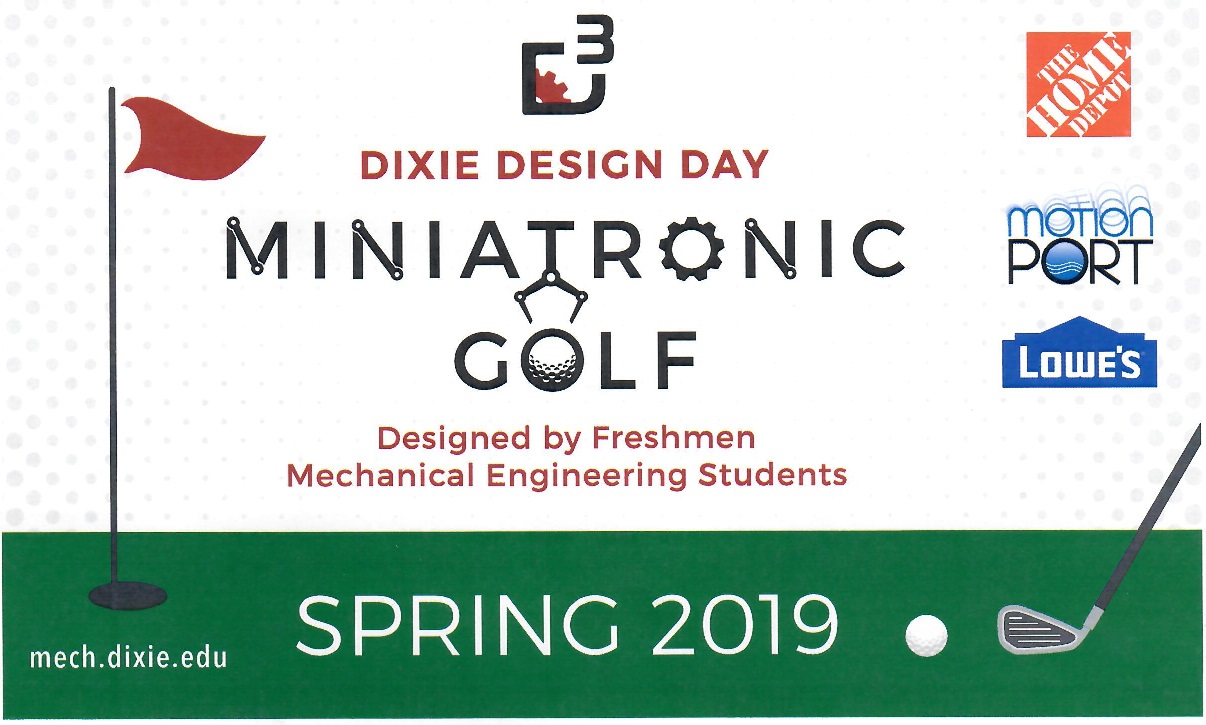
Design Elements Showcased
The design elements used in the holes varied in creativity, complexity, and ultimately in reliability. Some of the systems were quite ambitious.
For example, consider the ball lifting mechanism on the right. The golfer hits the ball up the ramp and into the holder. A sensor detects the ball and the holder lifts the ball to the top, where it is transferred to the black pipe and rolls down to the next section of the hole.
The concept was good, but the execution had some challenges. It is an interesting concept.
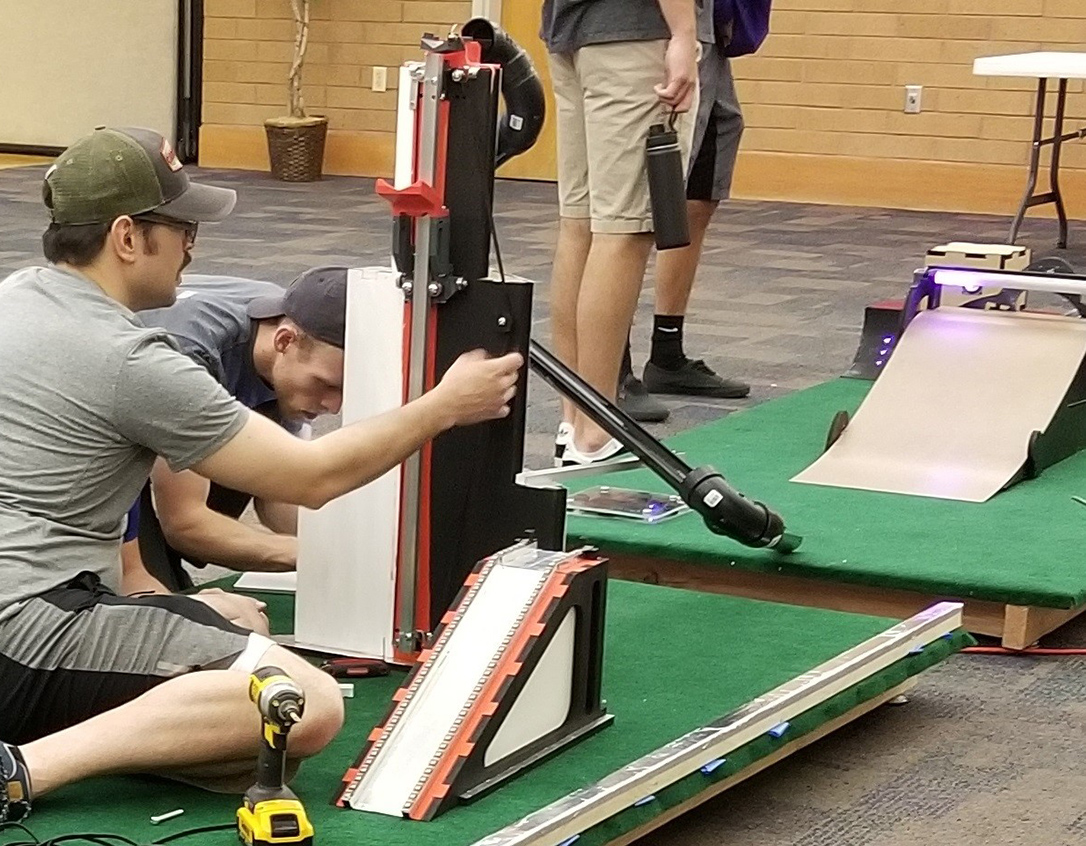
Judging before Grand Opening
Before the public got a chance to take the course through its paces, Brant got to visit with each group to learn more about the projects and how each individual member constructed their assigned section.
Judging consisted of scoring the following categories:
• level of completion
• adhering to the assigned theme
• interactive elements
• difficulty level of play
• design creativity
• safety
• overall presentation
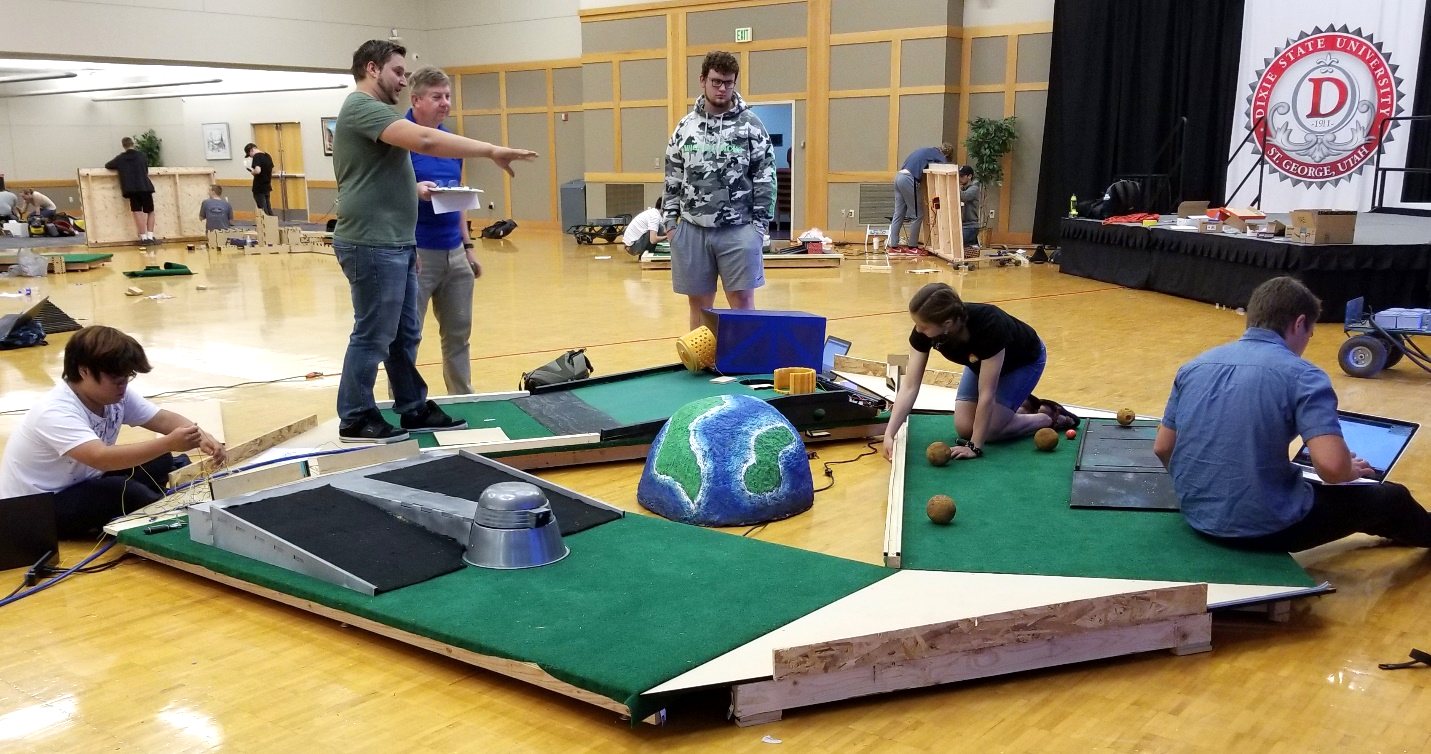
Brant reported that he really enjoyed seeing the creativity that the students brought to their work.
Bring in the Crowds!
After the judging was over, the public was allowed to participate in a round of putt-putt golf.
In attendance were college students, faculty, and staff; as well as families and friends from the community.
This was a great experience for the freshman students.
Although portions of their project did not work as planned, many things were working.
Most importantly, all of the students learned a lot.
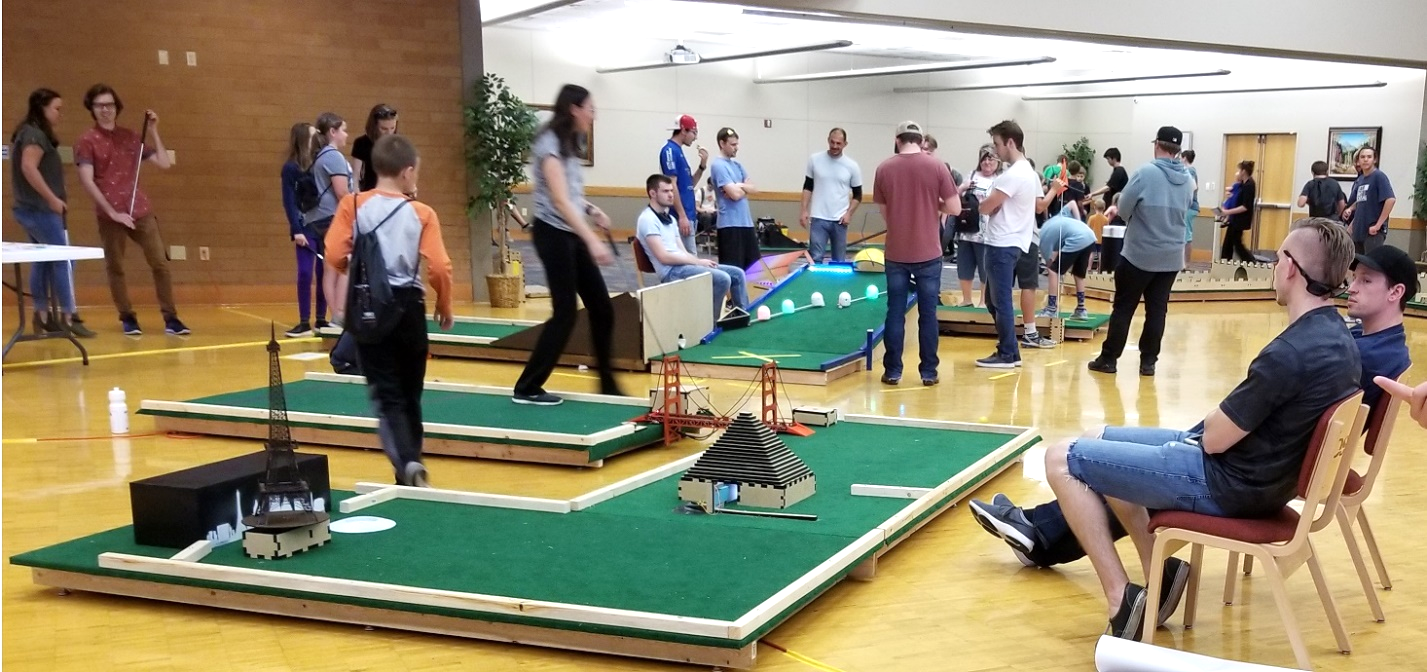
We can have high hopes that the senior design projects that these same students will be doing in three years will be really amazing, and will have their roots in this event.
All in all, DSU’s first Dixie Design Day was a real “hole-in-one”!
For more pictures of the Freshman design projects, please read the full article here.
RecurDyn News & Tips
A reminder about our 2019 users conference:
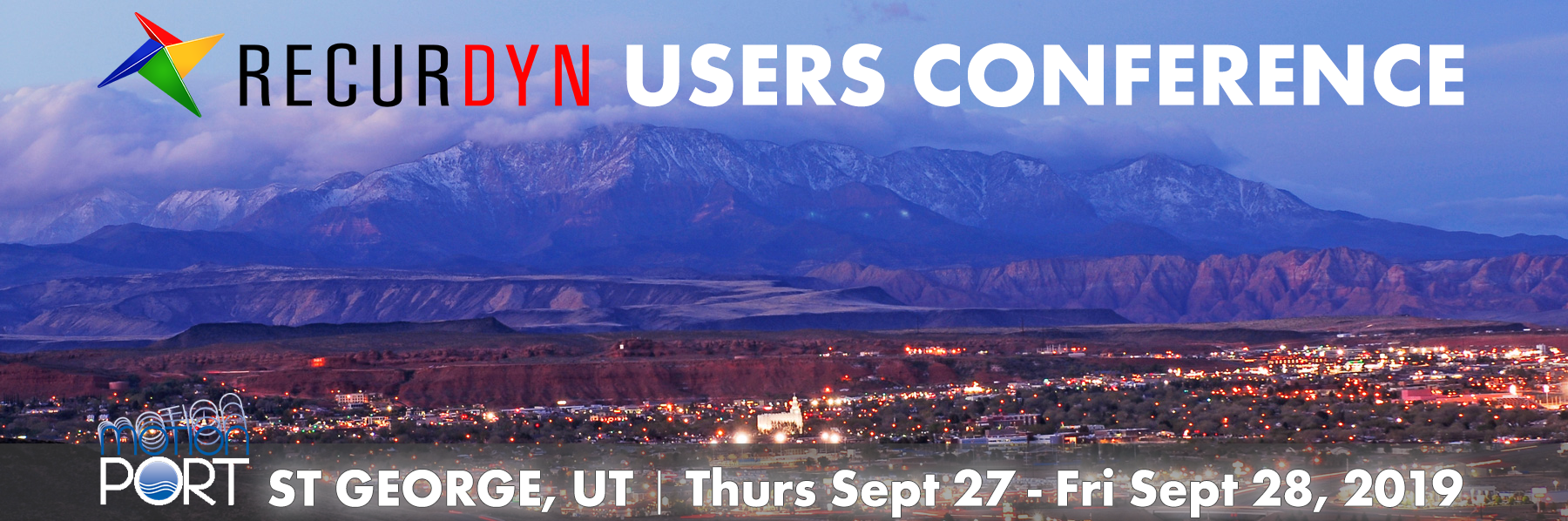
As announced in our previous newsletter, MotionPort will let you “have it your way” with the 2019 conference, given that it will be held both as an on-site conference at our headquarters in St. George, UT as well as a live streaming event. You can choose the option that works best for you!
At this year’s conference you will learn about RecurDyn V9R3 (to be released at the end of the summer), participate in hands-on learning, and interact with other users to gain insights. Please note that we will begin Thursday at 8:30 am MST and end Friday at 3:00 pm MST.
This event is FREE* to attend, register early to reserve your spot.
If you have already registered please note that we will be sending the agenda and more details in August.
User Tip:
How to use 'Scenario' Simulation Option when you need to adjust simulation and model details during the simulation.
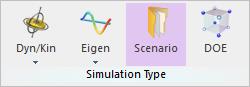
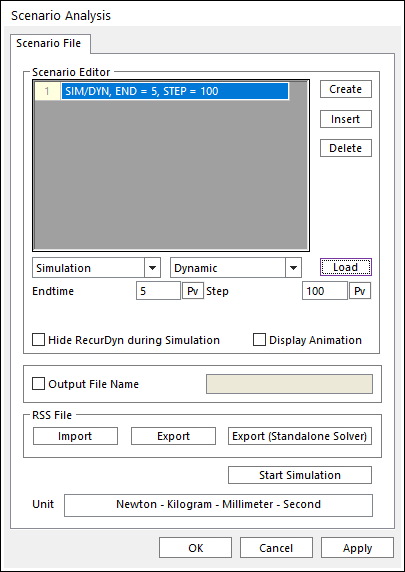
Scenario is a function to use when a model requires different simulation settings for specific time sections.
Click the Scenario icon of the Simulation Type group in the Analysis tab. The Scenario Analysis dialog box appears.
• Create: Creates the scenario command.
• Insert: Inserts the scenario command.
• Delete: Deletes the scenario command.
• Load: Loads the parameters of each analysis.
• End Time: Defines the end time of each analysis.
• Step: Defines the step of each analysis.
• Hide RecurDyn during Simulation: Refer to Hide RecurDyn during Simulation in Dynamic/ Kinematic Analysis
• Display Animation: If this option is checked, an animation is displayed during the simulation process.
◦ Note: In the case of Eigenvalue analysis, this option is not applied although this is checked.
• Output File Name
◦ If this option is checked, it allows defining the model output file name before simulation.
◦ If this option is not checked, the output file name will be the file name. (The default is not checked.)
• RSS File: RecurDyn SimulationScenarioFile: A *.rss file contains the information of the simulation process. You can export and import a scenario to *.rss.
◦ Export: Exports the *.rss file.
◦ Import: Imports the *.rss file.
◦ Export (Standalone Solver): Exports the *.rss file for Standalone Solver. Activate and Deactivate commands can be supported in Standalone Solver.
• Start Simulation: Runs a simulation with the specified Scenario.
To create scenario commands, use the following steps:
- Click the Create button.
- Select a command and a Type.
- Input the value of each parameter.
- Click the Load button.
- Click the Start Simulation button and the simulation is done as the scenario process.
For example, the entire simulation time is 12 seconds and you want to use different solver parameters for 3 different sections: 0~4 sec., 4~8 sec., 8~12 sec. You also want to activate or deactivate the specific force, contact or flexible body for each time section.
Here are the details:
1) 0~4 sec.: Dynamic analysis is performed with the axial force, ‘Axial1’ inactive (deactivated)
2) 4~8 sec.: Dynamic analysis is performed with the axial force, ‘Axial1’ active (activated)
3) 8~12 sec.: Dynamic analysis is performed with the contact, ‘SphereToSphere1’ inactive (deactivated)
Now, following the steps from above, create the parameters in the Scenario Editor as shown below:
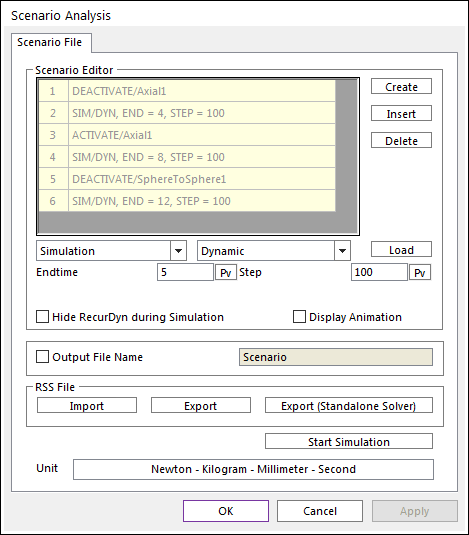
Once you have the parameters defined, click Start Simulation and the simulation will be done according to the scenario process you defined.
You can also find a related tutorial in the e-Learning section on the RecurDyn Technical Support site here:
https://support.functionbay.com/en/tutorial/single/58/professional-dipper-stick-bucket
You will need to login/register to view the content.
Want to learn more about how MotionPort can help you with your projects? Contact us today to schedule a free web meeting to learn how RecurDyn, Particleworks, and MBD for ANSYS are helping our clients and how they can help you.
MotionPort LLC | St. George, UT | www.motionport.com
Click here to unsubscribe